Para os setores automóvel, de eletrodomésticos e decoração de interiores
Projeto “Wood.Shape 4.0” junta indústrias da madeira e dos moldes na criação de novas peças
2022-03-31 10:37:30
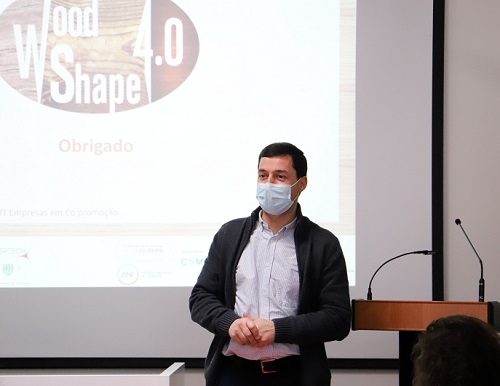
Florindo Gaspar
Surgiu da necessidade de valorizar um produto nacional, a folha de pinho, por parte da indústria florestal e da procura do setor industrial automóvel de novos produtos para segmentos de mercado mais exclusivos, valorizando o acabamento de peças interiores de automóveis e do setor de construção, procurando novos produtos com cada vez maior consciencialização ambiental e personalização. Falamos do projeto “Wood.Shape 4.0”, cujos resultados foram apresentados esta quarta-feira, dia 29 de março, no Centro para o Desenvolvimento Rápido e Sustentado de Produto (CDRSP) do Politécnico de Leiria, situado na Marinha Grande.
«Este projeto une duas indústrias de diferentes setores, florestal e moldes, cuja ligação não é muito habitual, mas ambas com tradição na zona de Leiria. O projeto visou a valorização de um recurso endógeno, a madeira de pinheiro-bravo, pela sua baixa condutividade térmica e aspeto visual, potenciando o valor comercial do produto e a sua customização em massa», começou por referir Florindo Gaspar, professor e investigador do CDRSP, na abertura da sessão.
«Através deste projeto procurámos o desenvolvimento de novos componentes injetados, de elevado valor acrescentado e com superfície estética de pinho. Recorremos, para isso, à tecnologia da conformação da madeira e do overmoulding, que até agora nunca tinha sido aplicado em madeira de pinho, auxiliadas de sistemas automatizados de visão computacional e integração de tags RFID [Radio-Frequency IDentification], com o objetivo de produzir peças com revestimento de folha de pinho e preenchimento polimérico de elevado valor acrescentado», acrescentou Florindo Gaspar.
A tecnologia de overmoulding é um processo bastante comum na indústria dos moldes e consiste na injeção de um polímero sobre outro tipo de material não-polimérico como metal, películas, filmes ou tecido. Através de técnicas inovadoras de moldação totalmente automatizadas, este projeto pretendeu fazer injeção sobre folha de madeira e madeira conformada num passo anterior.
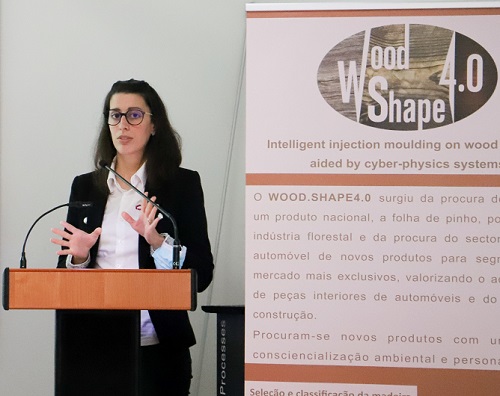
Nânci Alves
Iniciado em janeiro de 2018, o projeto resultou de um consórcio entre a TJ Moldes, o CDRSP, o Grupo Valco, o SerQ – Centro de Inovação e Competências da Floresta, a Universidade de Coimbra e as empresas AB Plásticos Batista e Makertech. O financiamento e orientação técnica foi da ANI – Agência Nacional de Inovação.
«Focando-se nos setores automóvel, de eletrodomésticos e decoração de interiores, este projeto procurou responder às necessidades sentidas pelos clientes, nomeadamente as constantes renovações de design com a valorização de materiais ecológicos, o desenvolvimento de novos produtos para segmentos de mercado mais exclusivos, a valorização da folha de pinho e a concretização de séries mais curtas. Além disso, focou-se também naquilo que o utilizador final mais valoriza: estética, preços baixos, sustentabilidade», apontou Nânci Alves, gestora de projetos IDI na TJ Moldes, numa apresentação sobre o tema “Desafio para os moldes”.
«Neste projeto centrámo-nos numa peça desenvolvida para um cliente, a partir da qual começámos a analisar o potencial da madeira e o que nos permitiria fazer, tendo havido a necessidade de ir simplificando o processo até termos o produto final. O maior desafio foi, efetivamente, conseguirmos fixar a folha de madeira. Isto porque as válvulas de vácuo não conseguiam fixar a folha de madeira, que no seu estado primitivo está plana, na posição vertical o tempo suficiente até que o molde fechasse», explicou Nânci Alves.
Como resultados do “Wood.Shape 4.0”, a gestora de projetos IDI na TJ Moldes destacou a redução de operações secundárias, a facilidade de rastreamento dos materiais utilizados para a sua substituição, a redução do número de estações de trabalho e do consumo de materiais auxiliares (óleos, massas, papel, etc.), e do tempo de ocupação de máquinas, entre outros.
Sob o mote “A relevância do projeto para a indústria”, Diana Duarte, responsável de inovação de processo na TJ Moldes, abordou o papel dos próprios clientes no desenvolvimento de novas peças. «Os nossos clientes têm-nos desafiado cada vez mais ao nível de design atrativo, adoção de novas metodologias de fabrico e de novos materiais, implementação de políticas “zero plástico”, garantir um custo otimizado e a diminuição da pegada de carbono, e o fabrico de produtos “amigos do ambiente”. É também neste contexto, que o setor da indústria de moldes deve avaliar as oportunidades de mercado e fazer propostas que possam trazer valor acrescentado aos clientes, nomeadamente o co-design», referiu.
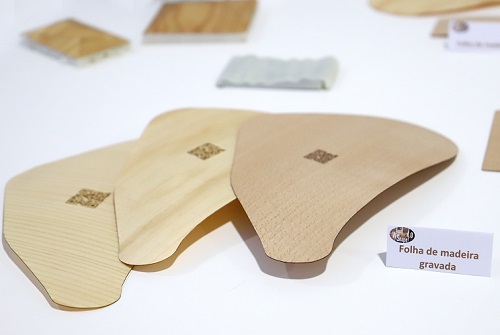
Molde de plástico revestido com folha de madeira
Como forças do projeto “Wood.Shape 4.0”, Diana Duarte destacou a aquisição de know-how para aplicação desta tecnologia, a utilização de materiais ecológicos, a redução de materiais como tintas e vernizes e a rastreabilidade de caracterização da peça, tendo apontado como fraqueza os custos para aquisição da linha de montagem e automatização do processo.
Por sua vez, enquanto oportunidades do projeto, a responsável de inovação de processo na TJ Moldes apontou uma nova abordagem à reciclagem da peça e a diferenciação com oferta de nova tecnologia para peças de valor acrescentado, tendo referido como ameaças o custo da peça final, a disponibilidade da madeira e a tecnologia disponível para a reciclagem da peça.
A sessão, que contou ainda com uma apresentação sobre a temática “Moldação por injeção inteligente em folha de madeira”, a cargo dos investigadores do CDRSP Francisco Diz e Liliana Gouveia, culminou com uma visita à exposição do projeto “Wood.Shape 4.0”.
Fonte: Midlandcom
Comentários:
Ainda não há comentários nenhuns.